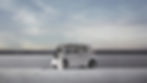
Solving the challenge of EV thermal systems
with FlowRithm run control logic and integration to thermal module hardware
TM
VALUE PROPOSITIONS
For the Customer / Driver:
- Drive Farther
- Reduced Waiting Time While Charging
- Confidence and Safety
For the OEM:
- Add predictive controls to next generation vehicles for more energy savings
- Support in launching first generation vehicles
- Less cost and resource by outsourcing run control logic and thermal systems

PRODUCT DEVELOPMENT
We take a holistic approach to first model then tailor a specific hardware and controls solution to OEM system requirements.
THERMAL MANAGEMENT
Unlike traditionally- powered vehicles, EVs have new and complex thermal management needs.
BATTERIES
Besides basic needs, cooling demands for DC Fast Charge and Extreme Fast Charge (XFC) are outpacing early "Level 1/Level 2" AC solutions. EV thermal management very commonly means using the minimum energy necessary to dissipate waste heat from charging batteries. Of course charging a battery is not 100% efficient. In an EV battery the electrons not effectively stored become waste heat that must be managed. The faster and higher power the charging the greater the heat dissipation challenge, and the industry is increasingly demanding faster charging.
​
​
HOT or COLD START-UP
In addition to removing excess thermal energy, EVs must also manage other conditions such cold or hot-climate start-up scenarios. Certain components in the vehicle may be "good to go" while others need warm-up or cool-down to perform or protect the system for long-term durability. Either maintaining an acceptable temperature (e.g. while plugged in) or quickly reaching an operating temperature at start-up requires complex decision making by smart thermal management controls.
CABIN COMFORT
While using electricity to run heaters or air conditioners is not new, deciding how high voltage components should integrate with the other EV vehicle systems for the most efficient operation is a new frontier. Energy management to enable the longest EV driving range is more complex than siphoning "waste heat" from an engine into a heater core. Whether the objective is to heat or cool a passenger compartment or defrost/defog windows the task has changed from decades of engine-based accessory controls.
DRIVE COMPONENTS and SYSTEMS
Batteries may be more sensitive to temperature for optimized performance but keeping motors, inverters, on-board chargers DC-DC converters and similar devices "cooled" often requires separate water-based cooling loops. To most efficiently manage the state of these components with flow control (e.g., versus the battery) can drive unique controls software for real-time vehicle-state decision-making.
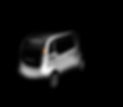
MODELING
Flow and thermal modeling creates the basis for efficient component selection and operating parameters. Either start with a "blank sheet" or bring your baseline assumptions or data to the task.


ARCHITECT SYSTEM HARDWARE
Use your thermal system, a third-party module; or, EVTFS can help choose thermal system building blocks such as water pumps, sensors, and valves.
Firmware that resides on the EVTFS controller creates a CAN-driven distributed thermal subsystem, off-loading VCU software, I/O and low-level diagnostics tasks for OEMs.
FlowRithm™ and THERMAL SCENARIO LIBRARY
-
EV Thermal Flow Solutions’ proprietary run control logic FlowRithm™ comprehends hundreds of run scenarios and commands the coolant pump speeds, flow directions, and CAN messaging to vehicle devices.
-
There is no needs to start from scratch; instead communicate to the EVTFS unit the top-down vehicle level commands and current state, and receive system status and run control direction